As a manufacturing leader, how do you manage the uncertainties of today’s volatile landscape? Geopolitical shifts and rising uncertainty in the global operating environment are significantly impacting industrial companies, creating challenges that ripple through supply chains and operations. Imagine waking up to find that a retaliatory tariff has suddenly added 145% to the cost of a critical component. Or, picture container ships idling outside the Panama Canal due to a drought that has slashed traffic by 36%. In just a few hours, your cost-to-serve spikes, promised lead times slip, and the production line hasn’t even started for Tuesday’s first shift. This is the reality of the manufacturing landscape in 2025, where global market disruptions impact your factory floor faster than your ERP can keep up.
The Challenge of Traditional Manufacturing
So, why is traditional manufacturing struggling to keep pace?
The reality is that the manufacturing landscape has undergone a dramatic transformation. Recent statistics reveal that global shipping delays can stretch up to 20 days, and production material lead times hover at a staggering 79 days—significantly higher than pre-pandemic levels. These figures highlight a critical question: How can manufacturers adapt to such rapid changes?
The answer lies in leveraging real-time data and AI-driven decision-making—not as a luxury but as a strategic necessity for building resilience and competitiveness. This raises another question: What does it mean to embrace operational intelligence (OI) in your organization?
Understanding Operational Intelligence: More Than Just a Buzzword
What exactly is operational intelligence, and why should you care?
Operational intelligence is not just another platform; it’s an evolutionary journey. It starts with standardizing processes and connecting assets through the Internet of Things (IoT), creating continuous streams of data. As you progress, real-time monitoring and advanced analytics powered by AI can transform operations from merely reactive firefighting to predictive maintenance and self-healing systems.
The manufacturing sector is undergoing a transformative shift, driven by the rapid adoption of generative AI. In just one year, from 2024 to 2025, spending on generative AI in manufacturing surged by 41%, reflecting the industry’s growing commitment to leveraging advanced technologies. This shift is not merely a trend but a clear indication of the industry’s evolution toward intelligent, data-driven operations.
The Pressure for Change: A Call to Action for Executives
We recognize that today’s executives prioritize efficiency and swift results in digital transformation initiatives. The board’s mandate is straightforward: “Cut costs, release cash, prove payback—fast.” But how can you navigate this environment effectively?
Let’s explore an actionable strategy to implement OI:
Starting Small, Winning Big: The Iterative Approach to OI
Here’s how to make OI work in today’s fast-paced environment:
Start where it hurts most
Identify chronic bottlenecks in your operations.
Focus on curbing energy cost overruns or addressing machines that consume more than their fair share of maintenance budgets.
Why is this important? Clarity at this stage helps secure stakeholder buy-in and ensures that your initial project tackles the highest-impact opportunity with immediate ROI potential.
Deploy focused projects
Implement projects within an 8–12-week timeframe.
Capture data, apply analytics, and embed solutions into daily routines.
What’s the benefit? This approach allows for a small pilot with incremental changes that require minimal change management but deliver concrete efficiency gains.
Bank and build
Document and bank the wins from your pilot projects.
Use savings to fund the next iteration, expanding your efforts based on proven ROI.
How do you measure success? Maybe you reduced downtime by 10% or saved up to 20% on energy costs—these victories will bolster support for future initiatives.
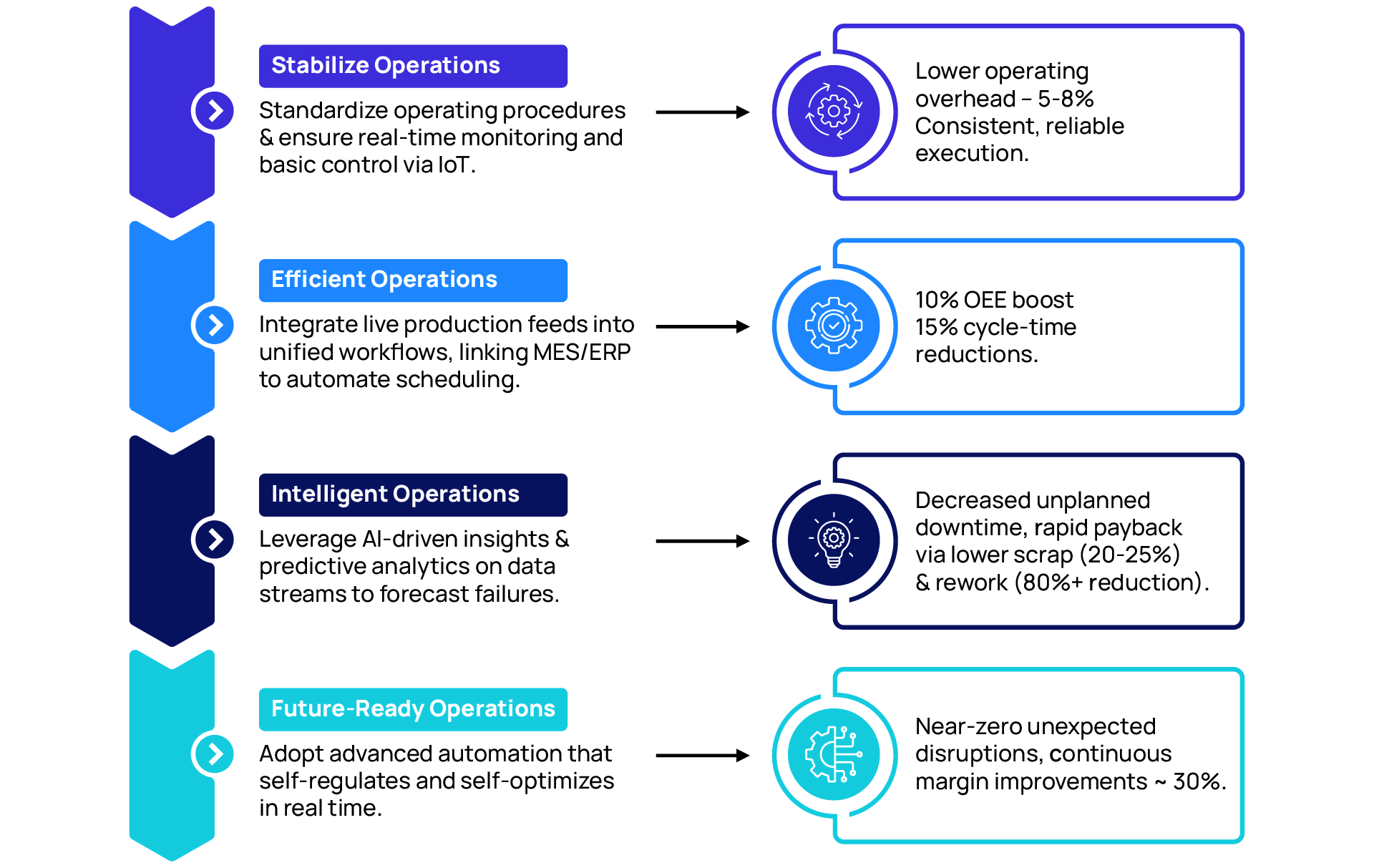
The Five-Step Journey to Operational Excellence
To successfully embark on your OI journey, consider these five steps:
Assess & discover
Start by baselining your operations.
Identify the most urgent cost drains or bottlenecks to target for a quick-win pilot.
Why is this crucial? Ensuring that your initial project addresses the highest-impact opportunity sets the stage for success.
Envision & blueprint
Define success metrics and scope the minimal viable solution.
Align stakeholders on budget, timeline, and deliverables.
How do you ensure alignment? By translating strategic goals into a feasible pilot plan, you build consensus on precise outcomes and data requirements.
Launch & learn
Execute an 8–12-week project—capture data, apply analytics, and integrate findings into daily routines.
What do you gain from this? Collecting tangible wins quickly demonstrates that OI investments yield clear payback, fueling momentum for broader changes.
Scale & integrate
Once your pilot proves successful, expand it across multiple lines or sites.
Unify data flows end-to-end and standardize processes enterprise-wide.
Why is scaling essential? Leveraging early ROI to fund larger transformations fosters cross-functional buy-in and breaks down operational silos.
Optimize & evolve
Introduce advanced AI for predictive and self-healing operations.
Explore new business models, such as usage-based services.
What’s the long-term vision? Sustain a continuous improvement loop, future-proof your enterprise, and keep driving bottom-line impact long after the pilot.
Emerging Technologies Reshaping Manufacturing Intelligence
What’s next on the horizon for manufacturing intelligence?
As organizations push for change at an unprecedented pace, several technological trends are emerging—ones that reshape entire enterprises at scale rather than remaining confined to siloed pilots.
Revolutionary Technologies to Embrace
Digital twin simulations
What are they? Beyond simple “what if” analytics, modern Digital Twins are robust virtual replicas of your end-to-end operations. They capture machine behavior, production line dynamics, logistics flows, and even workforce interactions.
How can they help? You can turn what used to be disruptive guesswork into smooth, iterative refinements that boost throughput, improve quality, and accelerate time to market.
What’s the next leap? While AI has fueled predictive maintenance and demand forecasting, the next evolution is “agentic” AI—autonomous decision-making engines that can ingest real-time data, dynamically learn from outcomes, and enact changes without waiting for human intervention.
What’s the impact? This drives immediate, high-speed orchestration that slashes response times, prevents costly domino effects from minor glitches, and positions the entire operation to handle complexity at scale.
Modular & vertical AI
What’s the difference? Modular AI acts as a digital conductor, coordinating tasks across separate systems like logistics, production scheduling, quality checks, and inventory planning. Vertical AI, on the other hand, targets a single domain in depth—for example, advanced machine vision for automated assembly lines in automotive manufacturing.
Why does this matter? By zeroing in on domain-specific knowledge and complexities, vertical AI solutions deliver potent, high-impact insights that address the most sensitive pain points, ensuring that every operational decision is both wide-ranging and finely tuned.
The Path Forward: Your Journey to Manufacturing Excellence
The manufacturing sector is at a crucial turning point. Have you considered how your organization can innovate amidst these changes? With construction spending in manufacturing reaching a record US$238 billion and over US$31 billion invested in clean-technology manufacturing facilities, the industry is primed for transformation.
Are you ready to turn disruption into opportunity?
By developing a tailored operational intelligence strategy, you can create a production environment that’s not just cost-effective but future-proof. The journey to manufacturing excellence starts with a single step—identifying where OI can make the biggest impact in your operations.
Conclusion: Embracing the Future of Manufacturing
The future of manufacturing is intelligent, adaptive, and data-driven. So, what’s stopping you from embracing operational intelligence?
In today’s manufacturing landscape, it’s not about whether to adopt OI but how quickly you can start reaping its benefits. According to an EY article, by 2030, 96% of companies are expected to increase their investments in manufacturing AI, and beyond 2030, 59% of industrial leaders will view AI as a significant game-changing force for the future of manufacturing.
Where will you position your organization in this new reality?
Investing in operational intelligence not only prepares you for today’s challenges but also sets the stage for long-term success. As you embark on this journey, remember: the integration of human intuition with advanced technology will unlock unprecedented efficiencies and opportunities.
Connect with our experts today to discover how operational intelligence solutions can transform your manufacturing operations and deliver measurable results within weeks!